Studies and energy performance contracts for industry
Do you have an investment project for which you want to take carbon impact into account? Are you planning to use a trusted third party to check that the performance commitment you have established with your supplier is being respected?
We will study your project in detail, taking into account your investment criteria, to determine a verifiable energy gain.
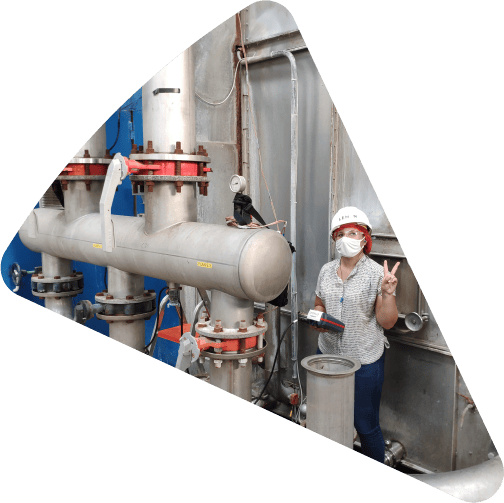
Improving the energy performance of industrial processes and utilities
We can help you improve the energy performance of your industrial processes and utilities.
When you plan your investments, integrating energy into the design and improvement of industrial processes brings considerable benefits.
Your investment in industrial process energy optimization pays for itself in energy savings. In addition to this return on investment, our services bring other benefits:
-
Lower operating costs
-
Compliance with regulations
-
Reducing carbon footprint
-
Improving product quality
A rigorous assessment of technological, regulatory and economic risks guides investments in industrial process optimization. Energy efficiency minimizes these risks.
ADEME monitors the studies it subsidizes. This control from the outset facilitates the financing of energy efficiency projects for industrial equipment, thus strengthening the investment guarantees for these projects.
We work independently with you to optimize your industrial processes through energy efficiency:
-
#1
Defining implementation scenarios
Define implementation scenarios, according to your criteria:
o Site production level
o Plant configuration
o Technology used
o Expected thermal levels
o Energy performance objectives and decarbonization of the site
o Energy supply -
#2
Evaluate potential energy savings
Model post-construction consumption to assess achievable energy savings, taking into account equipment operating conditions, influencing factors and site changes.
-
#3
Design and integrate solutions
Study the sizing and integration of solutions, in liaison with your technical teams and potential suppliers.
-
#4
Evaluate eligible financing
Initiate discussions with funding contacts for whom a solution is eligible.
On the basis of this study, we quantify the technical and economic benefits of a project, and the potential impact of its installation over its lifetime, including savings and operating costs.
Data analysis for industrial process improvement
We use data analysis to improve industrial processes. They guarantee results in terms of energy savings.
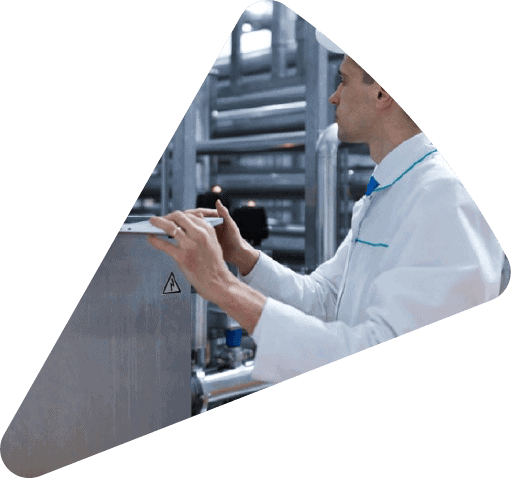
Verification of energy savings resulting from equipment or control changes can fail. The cause? A lack of means or methods, which can make it difficult to communicate successes to your management. To ensure that your objectives are met, it's essential to establish clear performance measures and follow-up mechanisms.
We draw up a plan for measuring and verifying your project's energy gains, and guide your project manager in setting up :
-
Energy performance indicators
-
Associated variables to be measured or collected by equipment type
We check the system's performance once the project has been commissioned.
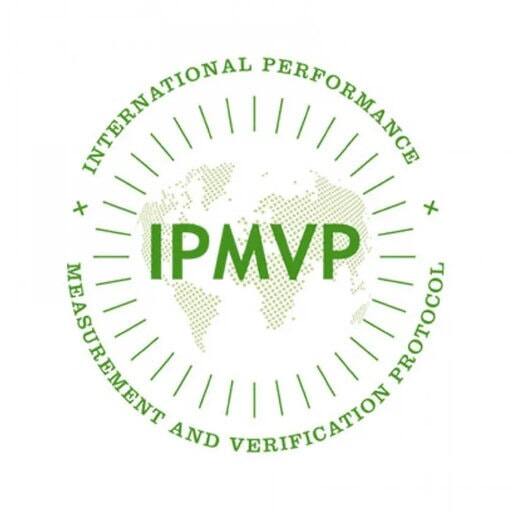
Our team's IPMVP qualification from AFNOR guarantees the reliability of our measurements. IPMVP is a protocol recognized in France by ADEME for measuring and verifying energy savings in buildings and industry. This protocol aims to put into perspective the energy savings achieved and the cost incurred to achieve them.
In order to regularly monitor and analyze the data linked to your installation, we offer performance commitment monitoring through the ZEST platform.
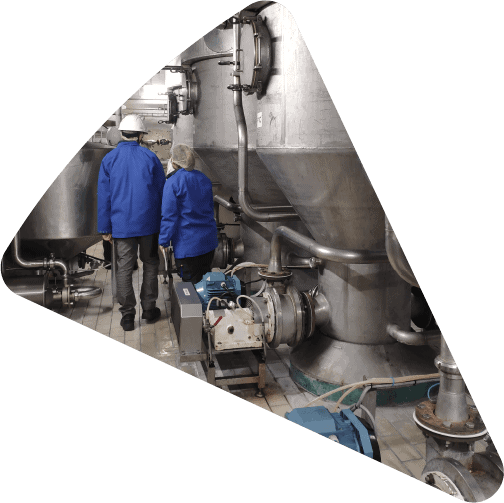
Energy performance contracting for a new plant or retrofit
In industry, an energy performance contract for a new plant or retrofit is a contractual agreement between you and a supplier. The supplier is remunerated according to the energy savings achieved.
The aim of an EPC is to commit to a project based on results (and not on the means employed), with the aim of reducing your energy consumption and improving the energy efficiency of your industrial facilities, while respecting a specified level of commitment.
Under this contract, in return for the supplier's installation of the solution, you agree to pay the supplier on the basis of the energy savings actually achieved.
We are involved throughout the EPC process:
-
When the contract is drawn up, to validate the calculation of the reference condition.
-
From commissioning, to check actual performance on a quarterly basis.
Case studies
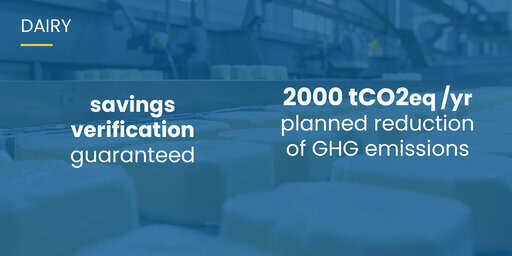
Heat recovery for a new production line
We drew up and monitored an Energy Performance Contract for a heat recovery installation on a refrigeration unit for a major dairy group. The project calls for savings of 2000 tCO2eq/year and the elimination of gas use, with guaranteed annual verification of savings achieved.
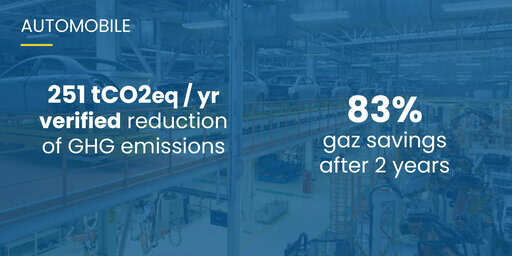
Monitoring a heat recovery system
We optimized the energy efficiency of an automotive equipment manufacturing plant by installing heat recovery solutions. Result: a clear improvement in employee comfort, 83% gas savings, 1307 MWh/year saved and 251 tCO2eq avoided, with quarterly meetings to ensure ongoing improvements.